Glazing estimation is a critical process in the construction industry, particularly for projects involving the installation of glass elements. This process entails calculating the costs associated with materials, labor, equipment, and other expenses necessary for glazing projects, including windows, storefronts, and vestibules.
The objective is to provide precise and competitive bids that ensure profitability while adhering to the client’s specifications and project requirements.
Accurate glazing estimation demands a blend of technical expertise, industry experience, and meticulous attention to detail. Estimators must be proficient in understanding various glazing systems, reading and interpreting blueprints, and staying updated on the latest material prices and labor rates.
The use of advanced software tools has further streamlined the estimation process, enhancing accuracy and efficiency.
Top 10 Best Practices for Glazing Estimation
- Verify the Quality of Project Plans
Ensure that the blueprints and project plans are comprehensive and accurate. If any information is missing or unclear, seek clarification from the architect or project manager.
Avoid guessing dimensions from scaled drawings as this can lead to significant errors in your estimates. For instance, accurately interpreting plans for a new storefront or a vestibule can significantly affect the project’s overall cost and feasibility.
- Detailed and Precise Takeoffs
Conduct accurate material takeoffs, ensuring all dimensions and quantities are correct. Miscalculations can result in either overestimating or underestimating, affecting the bid’s competitiveness and the project’s profitability.
Pay special attention to the types of glazing systems being used, such as curtain walls, windows, and glass doors.
- Keep Track of Price Changes
Regularly update your estimates to reflect current market conditions and price fluctuations for materials and labor. This includes staying informed about the prices of specific glazing materials like insulated glass units (IGUs), tempered glass, laminated glass, and specialty coating. At NM11 Constructions a record of all the price fluctuations is kept by a the Costing Department.
A holistic excel file has all the rates of all the product categories which makes our costing most up to date and enables you to be the most competitive bidder in the market.
- Use a Checklist
Utilize a comprehensive checklist to ensure all project aspects are accounted for. This helps prevent oversight and ensures that every necessary item, such as hardware, sealants, and accessories, is included in the estimate.
Customize your checklist for each specific project, adding notes and modifications as necessary.
- Understand Needs Before Costs
Clearly understand the specific glazing systems and materials required for the project. Determine any additional needs, such as special equipment for installing large curtain walls or packaging materials for shipping glass to out-of-town projects.
This understanding helps in accurately calculating both material and labor costs.
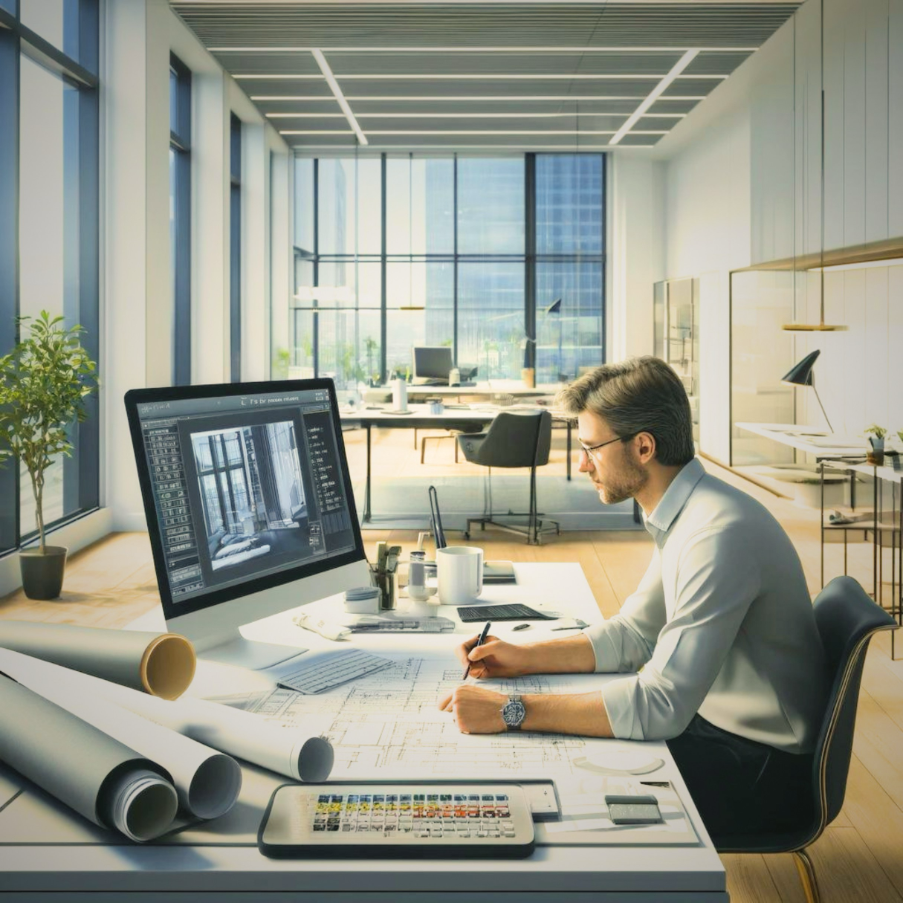
- Provide Detailed Descriptions
Ensure that every part of the estimate is detailed, especially in areas where you have less expertise. For example, provide detailed descriptions for custom glass types, edgework, and treatment processes.
This helps in identifying potential risks and mitigating them through accurate costing. Detailing specific requirements for windows, storefronts, and vestibules can also prevent miscommunication and errors.
- Ask Questions
Do not hesitate to ask questions whenever there is uncertainty. Consulting with more experienced estimators or individuals with hands-on experience in specific glazing applications, such as frameless glass doors or spider glazing, can provide valuable insights and help avoid costly mistakes.
- Leverage Technology
Use advanced estimating software to enhance accuracy and efficiency. Tools like Bluebeam, Pipedrive and PlanHub and other cloud-based platforms can optimize takeoffs, streamline proposal generation, and keep track of all project variables, ensuring a comprehensive and accurate estimate. These tools can also handle specific glazing configurations, such as point-supported systems and structural glazing.
- Factor in Contingencies
Always include a contingency allowance in your estimates to cover unexpected costs or changes in project scope. This buffer helps manage risks and ensures that you are not caught off guard by unforeseen expenses, such as delays in glass delivery or additional labor for complex installations.
- Review and Revise
Continuously review and revise your estimates. After submitting a bid, reflect on the process to identify any areas for improvement.
We provide the Glazing Estimation service by ensuring a holistic quality assurance process where each project estimator reports to a series of line managers ensuring strict compliance to quality.
Learning from each project also helps in refining your estimating practices and enhancing accuracy for future bids.
Consider feedback from project managers and installers regarding the practical aspects of the estimates, such as installation time and ease of handling. This is particularly important for projects involving complex elements like vestibules and custom storefronts.
Conclusion
Glazing estimation is an integral part of ensuring the success and profitability of glazing projects. By following these best practices, estimators can produce accurate, competitive, and comprehensive estimates that meet client expectations and support the smooth execution of projects.
Whether you’re a seasoned estimator or new to the field, implementing these strategies will help improve your estimating accuracy and efficiency, ultimately contributing to the growth and success of your business.
Please feel free to contact us at [email protected] for an obligation free assessment of your glazing estimation needs and a tailored glazing estimation service quote aligned with your landscape.